Comment fabriquer un iMac tout en aluminium, pourquoi observer à la loupe des têtes de vis, comment optimiser l'aimantation d'une Smart Cover et pourquoi des AirPods peuvent fonctionner avec une personne et pas avec une autre ?
La mise au point de nouveaux produits est un parcours semé d'embûches raconte John Ternus, le patron de l'ingénierie matérielle chez Apple. C'est un très long processus accompagné d'un travail d'équipe où la création d'une solution peut générer de nouvelles complications.
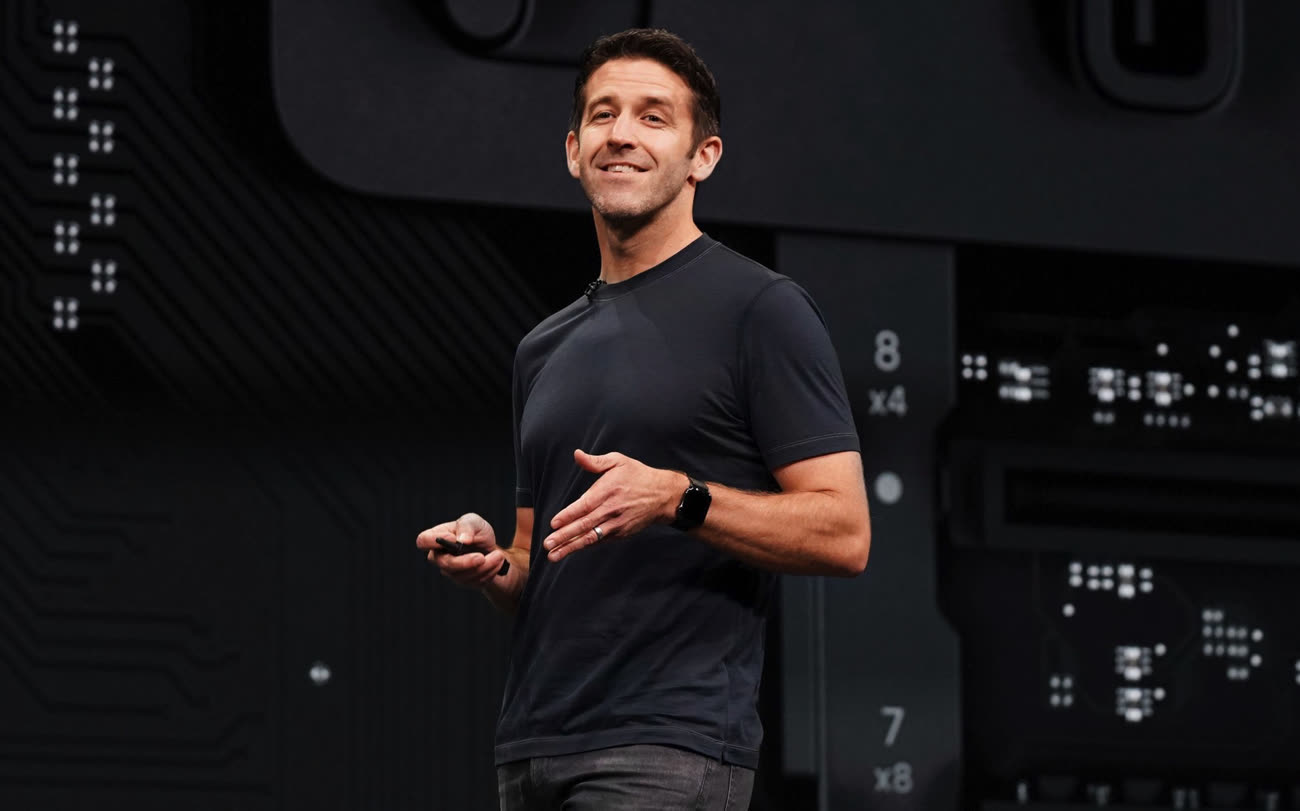
John Ternus est entré chez Apple en juillet 2001, il est depuis un an senior vice-président Hardware Engineering. C'est à lui qu'échoit la charge de dévoiler les nouveaux Mac lors des keynotes.
Dans une communication diffusée récemment en interne chez Apple, il raconte plusieurs anecdotes liées à la mise au point de quelques produits et les difficultés rencontrées. Elles illustrent les efforts qu'Apple peut déployer sur des aspects qui ne sont pourtant pas les plus essentiels d'un produit, en apparence du moins. En fond, il s'agit de montrer la nécessité d'une collaboration étroite entre équipes pour arriver à ses fins.
Châssis d'iMac
Premier exemple avec les iMac, dont on peut supposer que l'unique difficulté consiste à faire tenir l'électronique et l'écran dans un espace confiné avec les contraintes thermiques que cela suppose. Mais Apple voulait aussi pousser le bouchon un peu plus loin en renouvelant le châssis.
Jusqu'en 2006 les iMac utilisaient une enveloppe en polycarbonate, puis il y eut un modèle de transition associant une façade en aluminium et un dos en plastique noir. Pour la génération suivante de 2007, les designers d'Apple montrèrent à leurs collègues de l'ingénierie un prototype fait uniquement d'aluminium, devant comme derrière.
À cette époque, Apple travaillait sur de futurs MacBook Air et MacBook Pro dits « Unibody », en référence à leur procédé de fabrication. Leur châssis était patiemment usiné à partir d'un pavé d'aluminium afin de limiter le nombre de pièces à assembler et renforcer la structure (lire aussi Chroniques du SAV : l'Unibody).
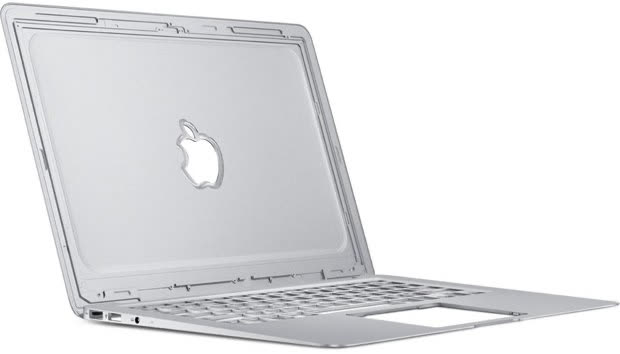
Le problème avec la nouvelle direction de style envisagée pour les iMac tenait dans leurs dimensions. Ces Mac grand format rendaient cette approche beaucoup plus compliquée.
Quelqu'un a fait un calcul rapide et a dit : "Eh bien, si nous devions faire la même chose pour ça [l'iMac], le bloc d'aluminium dépassera les 45 kg". Par conséquent c'était perdu d'avance, ce serait incroyablement coûteux, ça prendrait trop de temps et ce ne serait tout simplement pas pratique.