La conférence de présentation des derniers MacBook fut l'ocasion pour Jonathan Ive, le patron du design chez Apple, de faire l'article du nouveau procédé de fabrication employé avec ces machines. Il est rare qu'Apple s'attarde sur cet aspect. Le nouveau processus, aujourd'hui élargi à tous ses portables, fut inauguré avec le MacBok Air.
Ive a rappelé les contraintes posées par la réalisation d'un portable qui doit allier des traits antinomiques : finesse et légèreté, mais robustesse et solidité. Puis de développer le procédé employé jusqu'à présent. Il consistait en l'assemblage de plusieurs éléments qui s'épaulent les uns les autres. On part d'une armature formée de nombreuses pièces qui additionnées composent la charpente du portable.

Ensuite les éléments extérieurs du châssis et une plaque viennent l'habiller et enfin une pièce de plastique va faire la jonction avec le repose poignets et le châssis inférieur.
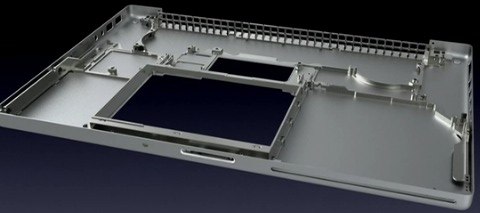

Une approche qui entraine une certaine complexité, des risques de défaut sur l'une des pièces, un surcroit de poids et des limites dans le travail sur la finesse. Autant de pierres d'achoppement pour la conception du MacBook Air. Celui-ci devait être rendu plus fin et léger que les modèles conçus jusque-là par Apple, mais en conservant des qualités de rigidité.

Les designers d'Apple sont donc partis d'une unique pièce d'aluminium, progressivement usinée par laser et sur machines outils (voir la vidéo), pour former, au bout de 13 opérations, le repose poignet du MacBook Air, avec ses logements pour le clavier et les vis. Soit une seule pièce là où il en aurait fallu bien davantage. Ce qu'Apple désigne par un "châssis unibody".

Dans le cas du MacBook Air, la plaque de métal de départ pèserait 1,13 Kg pour être ramenée à 113 grammes. Et Ive d'insister sur la qualité recyclable de l'aluminium où tous les déchets résultant de cet usinage sont récupérés et réutilisés. On remarquera d'ailleurs que la notion d'environnement est devenue un critère à part entière dans l'argumentaire d'Apple, au point d'être clairement mis en avant.

Ive a rappelé les contraintes posées par la réalisation d'un portable qui doit allier des traits antinomiques : finesse et légèreté, mais robustesse et solidité. Puis de développer le procédé employé jusqu'à présent. Il consistait en l'assemblage de plusieurs éléments qui s'épaulent les uns les autres. On part d'une armature formée de nombreuses pièces qui additionnées composent la charpente du portable.

Ensuite les éléments extérieurs du châssis et une plaque viennent l'habiller et enfin une pièce de plastique va faire la jonction avec le repose poignets et le châssis inférieur.
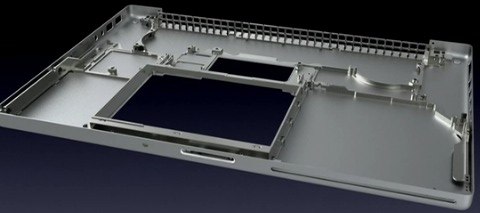

Une approche qui entraine une certaine complexité, des risques de défaut sur l'une des pièces, un surcroit de poids et des limites dans le travail sur la finesse. Autant de pierres d'achoppement pour la conception du MacBook Air. Celui-ci devait être rendu plus fin et léger que les modèles conçus jusque-là par Apple, mais en conservant des qualités de rigidité.

Les designers d'Apple sont donc partis d'une unique pièce d'aluminium, progressivement usinée par laser et sur machines outils (voir la vidéo), pour former, au bout de 13 opérations, le repose poignet du MacBook Air, avec ses logements pour le clavier et les vis. Soit une seule pièce là où il en aurait fallu bien davantage. Ce qu'Apple désigne par un "châssis unibody".

Dans le cas du MacBook Air, la plaque de métal de départ pèserait 1,13 Kg pour être ramenée à 113 grammes. Et Ive d'insister sur la qualité recyclable de l'aluminium où tous les déchets résultant de cet usinage sont récupérés et réutilisés. On remarquera d'ailleurs que la notion d'environnement est devenue un critère à part entière dans l'argumentaire d'Apple, au point d'être clairement mis en avant.
